Worthy of NoticeOne of continuing vulnerability of the No. 2
drill was the way main handle was attached to the frame.
This vulnerability manifested itself in cracks of the handle at
the point of attachment to the frame. It is especially
notorious on the drills introduced sometime after 1906 when
thicker handles were implemented, following changes in the frame
design. The new handle was much thicker at the point of
attachment to the frame and carried wider, stepped ferrule.
Here are some pictures showing the problem on
drill from c. 1938.
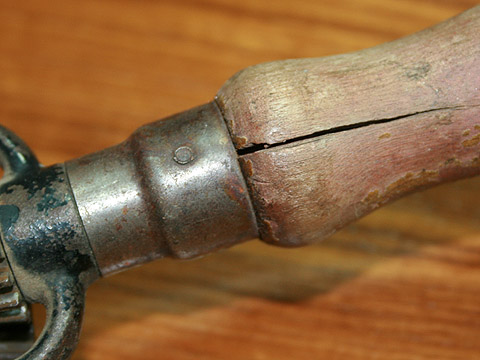
There are a variety of reasons for this persistent vulnerability and
they are analyzed in depth by George Langford in his No. 2 drill
type study. Spend some time on his web site at
GeorgesBasement.com - well worth it! In addition to
his finding, I believe there is one more reason for this
problem.
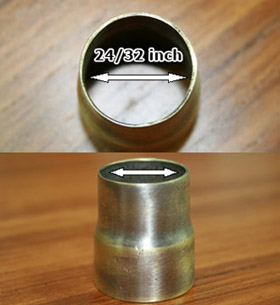
The outside diameter of the frame end, the tenon, is 20/32 inch but the
inside diameter of the ferrule is 24/32 inch. In addition,
the casting of this tenon does not have a sharp, 90 degrees
angle to the edge of the frame and existing
slope prevents a ferrule to fit snugly.
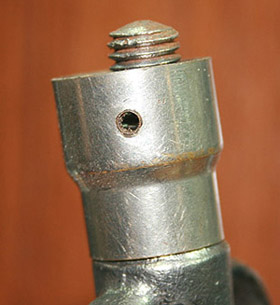
Consequently, the ferrule is a free-floating part that does not
serve its purpose. I believe
these parts should fit tight to each other and do not leave any
wiggle room. However, it is not the case on drills I have
examined. This creates overall pressures
distribution problem during the drill use.
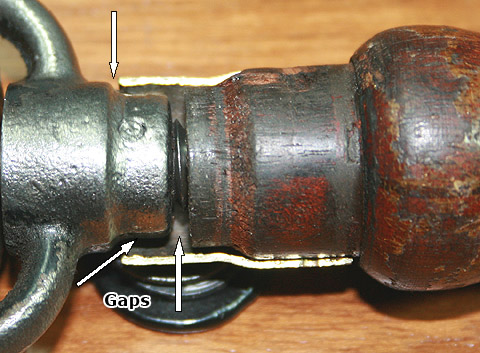
Here is a cut-out of the assembly. As you can see,
the work of controlling the drill is performed only by the
wooden handle attached to the threaded rod, without any support
from the ferrule or surfaces of the tenon and wood of the handle
touching together. In correct design and execution these gaps would be eliminated and provide
for much better distribution of pressure on wooden handle.