Hack Saw History
The story of Star Hack Saw Blades is a long
romance by itself - too long to more than touch upon here.
Previous to 1880, the only saw used for cutting metal was one
known as Stubbs’ and imported from England. This was dulled
after a few cuts and required frequent filing at the cost of a
dozen present-day hack saw blades.
The originators of Star Hack Saws were Yankees and held their
thumb on the weak feature of the Stubbs - the filing. Why not
make a saw blade so highly tempered that it could be dulled only
with difficulty, and so tough that it offered a reasonable
resistance to breaking?
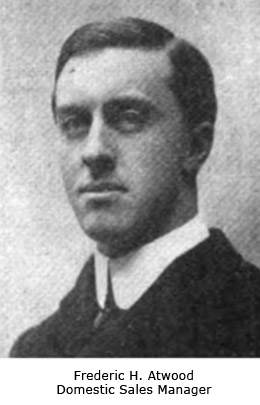
Some attempts had already been made in this
direction, but the problem of getting just the right saw blades
was a difficult one; there was a provoking lack of uniformity
and there were discouraging obstacles in the way of simplifying
the manufacture, but the Millers Falls Co. had its Edison who
threw his life into the work and the company was soon able to
guarantee absolute uniformity of saw blades and later so
systematized the process of making as to cut the cost to a small
percentage of what it originally was.
The formula of the steel from which Star Hack
Saws are made went through about as many changes as years have
elapsed since their introduction, always for the better.
Other brands of hack saws there were. The fact
that they were alike to the eye was conducive to making their
name Legion. With the ardor of conviction, the gauntlet was
thrown down before other makers, and the challenge made to cut
off with one Star saw more than could be cut with a dozen of any
other brand. For whatever reasons it is not known, but only one
contestant, at present a manufacturer with some reputation had
the temerity to appear. It was a man's job to put the contest
through. Coats were thrown off and sleeves rolled up.
The Star pusher was a husky man with a husky
blade, and not only cut as much as his opponent with a dozen
blades, but then bundled the latter, and with the same blade
sawed the whole dozen in two.
Some Other Machines
Among the earlier products of the Millers Falls
Co. were machines variously known as jig, fret, scroll or
bracket sawing machines. These were added to the company's
products as a “fill-in” to keep the plant busy in the autumn
when trade on other items languished.
The machines were, in fact, preceded in 1872 by
hand frames intended for the same purpose. These quickly
suggested foot-driven machines, which have enjoyed an immense
popularity. They were the means of carrying the Millers Falls
Co.’s name into households in all corners of this country and it
is a common saying on the part of grown men, “Why, yes! Millers
Falls Co.?
I had one of their fret saw machines when a boy and
it has now been brought down from the attic for my grandson.”
Perry Mason & Cot, publishers of Youth's
Companion, used these machines in their premium lists from the
start, and were largely instrumental in building up a demand.
At no time have the company curtailed growth in the way of
adding new tools to the line. Naturally, the result of fifty
years is a very diversified product.
Bit braces, hand and breast drills, hack saws,
and miter boxes comprise the major lines, but equal care has
been exercised and success attained in making not only other
tools as mentioned in the foregoing, but also boring machines,
chain drills, automatic push borers, soldering coppers jack
screws, vises, etc., etc.
A Large Variety
From the first, the officers and guiding heads
of the company have stuck fast to the idea that there was a
demand in the United States alone for all of the best of the
kinds of tools it already made or might originate, and that
there should never be any deterioration in quality.
Accordingly, improvements in design and quality
have constantly been added so dealers have generally expressed
pleasure at getting Millers Falls tools for the sake of
improvements all the time without any addition in price. At no
time have more improvements been under way than at present.
Similarly, the appearance of all tools placed on
the market by the company has been studied carefully so that
they bear a most-attractive and distinctive tone.
A hammer is a hammer to many men, and a bit brace, a bit brace,
but the Millers Falls Co. are making two hundred and fifty four
different bit braces and seventy-five different hand and breast
drills. In passing, it should be mentioned that there is always
on hand for the making of the wooden parts of these and other
tools, four hundred tons of rare and costly quantities of native
woods.
Following It Through
It would take many pages to follow in detail the
course of a single tool such as a bit brace from raw material to
the finished product in the shipping room. Let a carpenter
consider that his bit brace if of the Millers Falls Co.’s most
up-to-date style has undergone two hundred and twenty-four
distinct operations and that it has gone through almost as many
hands. Such is the case. The history of a single part will serve
to illustrate what this means. For example, the so called
alligator jaws.
The raw stock is in the form of bars of
carbonized steel. This is thrust into a forge and when brought
to a white heat is held beneath a heavy drop hammer that stamps
out the shape of the jaw. The rough jaw is then cut off and sent
to the annealing furnaces, where a certain temperature is
carefully maintained. Next the jaw is cooled slowly to make
workable. This process is handled carefully so as to leave the
jaws with all their proper toughness.
The sides of the jaw are then machined to the
proper width, the teeth are milled, holes drilled for spring and
pin at the base. A special hardening process next takes place,
then polishing on emery wheels; nickeling and the inserting of
pin and wire spring. The jaw is now completed and after
inspection is stored with other finished parts until called for
by the assemblers. Incidentally, the company’s stock of finished
parts amounts to over thirty thousand different kinds.
Through Several Generations
The company has been fortunate in having
associated with it a large number of competent young men who are
instilled with the best traditions of the business. A similar
spirit has served to imbue every workman of the company with the
thought that the best in tools is none too good. Many of these
workmen have been with the company since its beginning.
In one case grandfather, father and son are
actively employed. The grandfather works in the same room over
which his son is foreman.
While this is being written we learn that one of
the company’s tool makers at the age of eighty years, after
forty-five years of service, not only with the Millers Falls
Co., but as a fellow-workman at the bench with Messrs. Gunn and
Amidon at the Greenfield Tool Co., packed his kit, shouldered
his chest and, shaking hands with his fellow-workmen, quietly
left the factory. He intends to spend his remaining years on a
flourishing farm that he has been developing for years. The
company invited him to continue indefinitely, but he had always
determined to retire at the age of eighty.