Indeed, the
mechanical appliances for finishing and adjusting different
parts, comprise one of the most interesting departments of the
works, with their planting machines, lathes, punches,
screw-cutting tools, grinding and polishing stones, and drills
which allow of the drilling of several holes in the same piece
at the same time, and at various angles.
The pig iron
used preferably for malleable castings is a white charcoal pig,
and is melted in cupolas, or in a reverberatory furnace (picture
below).
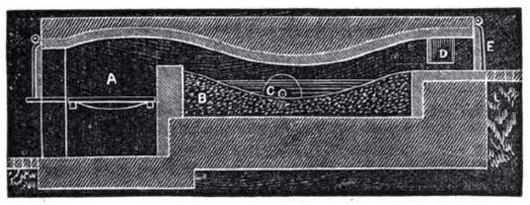
This latter
furnace, of which A is the fire-place, B the hearth, 0 the
tap-hole, D the flue towards the stack, and E the door through
which the impurities are removed from the top of the molten
metal, consumes more fuel, and produces more waste than the
cupola. On the other hand, the metal is purer, because it is not
melted in direct contact with the fuel, and does not absorb its
impurities, sulphur especially. There is also the advantage
that, should the metal contain too much carbon, part of it may
be removed by the oxidizing action of the flame.
Most of the
castings are made in green sand, from metallic patterns, which
insure constancy of shape and of smooth surfaces.
The castings,
which are as brittle as glass, are then put into "tumblers,"
which are revolving cylinders of cast-iron with ribs inside, in
which the articles are deprived of adhering sand, and become
polished by mutual friction.
The cleaned castings, intended
for conversion into malleable iron, are next packed close, with
alternate layers of powdered iron scales from rolling-mills,
into rectangular cast-iron boxes D (engraving below), which
become of a rather elliptic shape, after a certain length of
use, and which can be placed one upon top of the other, if need
be, and closed at the top by a mixture of sand and clay which
prevents contact with the air, and follows the settling of the
mass.
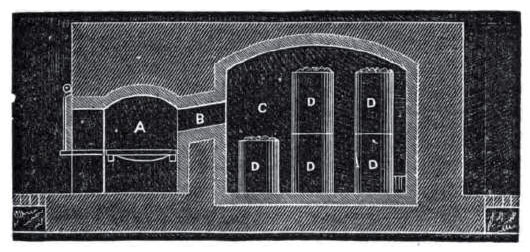
Engraving above represents the disposition of
the annealing furnace, which resembles those employed for making
the bone-black of sugar refineries. A is the fire-place, B a
flue conducting the flame into the annealing chamber C; and D D
D are the cast iron boxes filled with the iron scales and the
articles to be softened.
Leaving aside the time necessary for raising the
temperature, and the cooling off, the articles are subjected for
about a week to a white heat, not sufficient, however, to melt
what may still remain of cast-iron.
After a proper annealing, the castings are
covered with a film of oxide of iridescent colors - the yellow
and azure blue predominating - which resembles that kind of
Champlain iron ore called peacock, on account of its coloration.
Any adherent oxide is removed by another passage
through the "tumblers," and the process of malleable iron making
is finished. Any further grinding, polishing, boring, and
adjusting which may be needed, is made in the same works.
The oxide of iron, or scales, employed, have
parted with a portion of their oxygen during the annealing
process, and the loss is made good by grinding the scales, and
rusting them with a solution of sal ammoniac (hydrochlorate of
ammonia).
It seems to us possible to do without the
expense of sal ammoniac, by wetting the powdered scales several
times with water, stirring and drying them on the top of the
annealing furnace.
Among the products manufactured by the above
mentioned firm, we have noticed hinges, entirely of cast-iron,
and others with wrought iron pivots; patent elastic washers for
railroad fish-plates, which prevent the nut from unscrewing, and
keep it tight; castors for furniture, bolts, pulleys for cords
of window sashes, keys, padlocks, screw presses, carriage parts,
saddlery hardware, &c. &c. In fact, it would be necessary to
make a catalogue with an index, of all of the patterns which
were shown to us.
It is difficult to state the cost of malleable
iron castings, since it depends to a great extent upon the size
and the quantity of the articles. We may say, however, that
being given a certain pattern, the malleable iron castings will
cost from 70 to 80 per cent, more than ordinary castings from
the same pattern. This increase of price is necessitated by more
labor, the consumption of fuel for annealing, greater cost of
pig metal employed, &c. &c.
To sum up, malleable iron castings are useful,
whenever equal strength of material being not needed, the cost
in labor, if made of wrought iron, would be too great; or when a
casting is needed without the brittleness of common cast iron.
Scissors, sewing-machine parts, the butt-ends
and guards, and many other parts of gun locks, ornaments, &c.
&c, are made in quantities from malleable iron castings. Even
nails, of all sizes, are thus manufactured in England, and we
are disposed to believe that, if made of good metal and well
annealed, they may be at least equal to certain cut-nails
produced from inferior plate, and the fiber of which has been
broken by the concussion of the cutting machine.
Oxide of zinc has been proposed as a substitute
for oxide of iron, under the plea that the operation is more
rapid.