The manufacture of malleable
iron castings is older than is generally thought, although the
knowledge of the true principles on which it is based dates from
the more recent period of the establishment of chemical science.
In his work on the "Art of Converting Wrought Iron into Steel,
and of Softening Cast-iron" (Tart deconvertir le fer forge en
acier, et Tart d'adoucir fe fer fondu), published in 1722,
Reaumur gives the numerous experiments by which he succeeded in
producing malleable iron castings, which had already been made
some twenty years before, but in a secret manner.
At the epoch in
which Reaumur lived, the true era of chemistry had not yet
begun, the relations of carbon to iron in pig metal were not
known, and the various degrees of hardness and appearance in
cast-iron were attributed to the presence of various impurities,
sulphur especially.
After many
experiments with all kinds of substances and salts - the results
of which were noted with a remarkable acuteness of observation -
Reaumur succeeded in his purpose with three different mixtures.
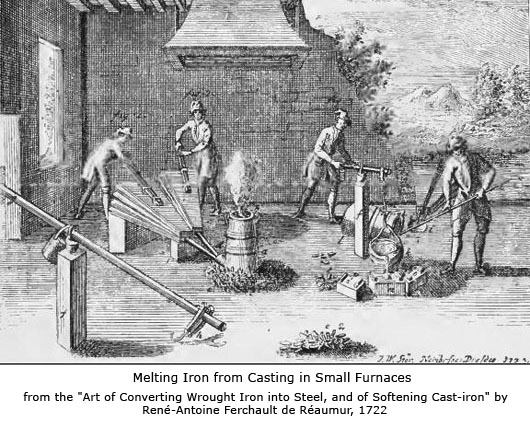
Having observed
that a plate of cast-iron, exposed for a long time to the direct
action of a fire, was covered with a coat of black and red
oxide, and that the metal underneath had become softened
(malleable), he collected such oxide for the purpose of packing
with it small bars of white cast-iron, and after heating them in
covered crucibles, he obtained a perfectly malleable iron. His
other mixtures were powdered limestone and charcoal, and
charcoal with calcined bone-dust.
The first
mixture is evidently that used at the present time; the second
may be explained by the oxidizing action, at a certain
temperature of the carbonic acid disengaged, which parts with an
atom of oxygen (CO2 + C = 2 CO) combining with the carbon of the
cast iron, and which becomes carbonic oxide. In the third case,
we may surmise that the carbon was burned out by the air of the
fire-place, penetrating through the interstices of the cast iron
plates forming the boxes in which the metal and the mixture were
packed.
The air was
prevented from acting violently by the mass of bone-dust and
powdered charcoal with which the articles were surrounded. We do
not believe that the temperature was sufficiently high to
decompose the bone dust, even in presence of the charcoal.
The furnace
employed was of brick, and square, and divided by vertical
partitions of cast-iron plates, between two of which were packed
the castings and the mixture, and around which were flues far
the circulation of the gases of the fire-place.
However
imperfect these dispositions may be when compared with the
present ones, Reaumur ascertained that oxides of iron and
cast-iron, heated together in closed vessels, produced malleable
iron; that for malleable castings, white is preferable to gray
metal; that the castings, previous to annealing, should be
deprived of the adhering sand, which becoming fluxed, prevented
the reaction; that too protracted and too intense a heat may
harden the castings again; and that properly annealed articles
may be bent, forged, welded, case-hardened, and present all the
properties and even appearance of wrought iron.
After having
explained the principles upon which the industry of malleable
iron casting is founded, and given a historical notice of the
first trials made, we cannot do better than to describe the
actual processes, such as are applied at the Hardware and
Malleable Iron Works of Messrs. Chas W. Carr, Jos. S. Crawley,
and Thos. Devlin, successors to E. Hall Ogden, and whose store
is at 307 Arch Street, Philadelphia.
In this large
establishment, where everything is conducted with the best order
and understanding, anything in the line of ordinary and
malleable castings for building and cabinet, carriage and
saddlery hardware, &c., is made complete, from the pattern to
the casting, annealing, coppering, adjusting and japanning of
the articles.
